Universeller freikonfigurierbarer Arbeitsplatz
Der universelle freikonfigurierbare Arbeitsplatz UfA aus dem Hause boschen & oetting bietet die Möglichkeit aus einer großen Auswahl von Komponenten einen ergonomischen, effizienten und kostengünstigen Arbeitsplatz zusammenzustellen. Prozesse lassen sich ohne Programmierkenntnisse konfigurieren. Komponenten können schnell und einfach ausgetauscht oder hinzugefügt werden. Montageschritte können einfach ergänzt oder von einem auf den anderen Arbeitsplatz portiert werden. So kann schnell auf Änderungen des Produktes reagiert werden ohne das Softwareänderungen an der SPS durchgeführt werden müssen.
Auswahl möglicher Komponenten:
- Schraubeinheit
- Fügeeinheit
- Nieteinheit
- MRK-Roboter (Mensch-Roboter-Kollaboration)
- Pick-by-Light
- Kamera zur Objekterkennung (Vision Sensor)
- Codeleser (1D/2D)
- Zylinder (pneumatisch)
- Etiketten-Drucker
- Beschriftungsgeräte
Beim Einsatz dieser Komponenten sind keine Softwareänderungen nötig.
Es ist auch möglich Fremdapplikationen wie z.B. Dichtmittelauftrag zu implementieren.
Die Arbeitsplätze sind wahlweise als Handarbeitsplätze oder beispielsweise über ein Transportband als verkettete Linienarbeitsplätze konfigurierbar.
Prozess- und Qualitätsdaten können auf einem boschen & oetting Anlagenrechner oder auf kundeneigenen Systemen erfasst und protokolliert werden.
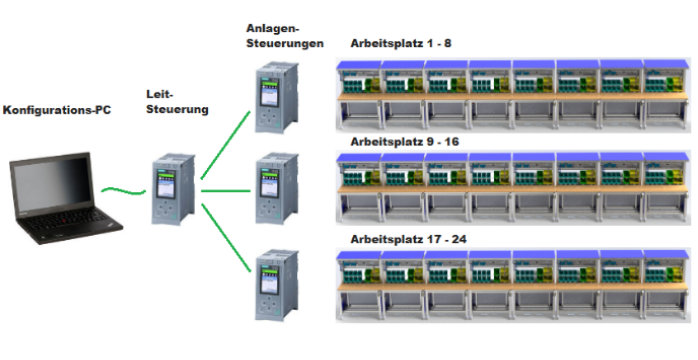
Abbildung 1: Anlage groß - mit mehr als acht Arbeitsplätzen
Anlagenstruktur
Prozesse und Operationen werden über einen Konfigurator definiert und auf eine Leit-Steuerung übertragen. Diese weist dann den Anlagensteuerungen die jeweiligen Operationen zu. Jede Anlagensteuerung kann bis zu acht Arbeitsplätze verwalten. Bei kleineren Montagelinien kann die Anlagensteuerung die Funktion der Leitsteuerung mit übernehmen.
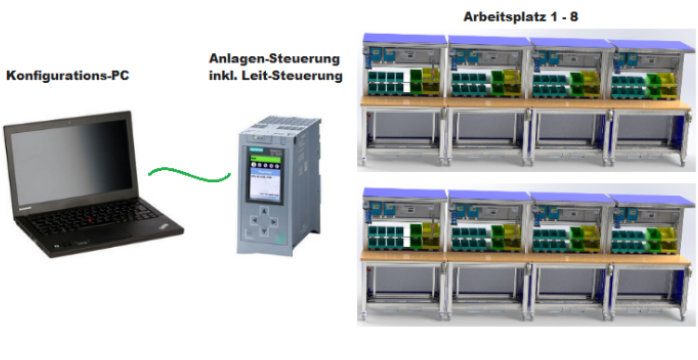
Abbildung 2: Anlage klein - bis acht Arbeitsplätze
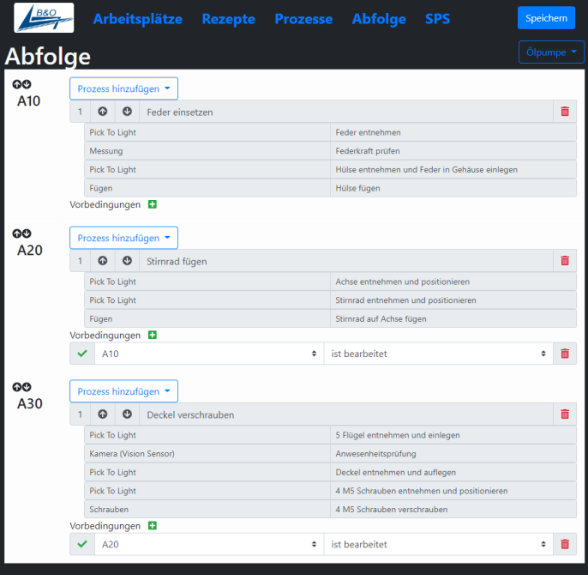
Abbildung 3: Konfiguration der Prozessabfolge
Konfiguration
Die Konfiguration findet über eine moderne Webapplikation statt, die bequem mittels Webbrowser bedient werden kann. Der Konfigurator kann auf einem beliebigen Rechner ausgeführt werden. Eine Verbindung zur Anlagensteuerung ist nur notwendig, um die Konfiguration zu übertragen.
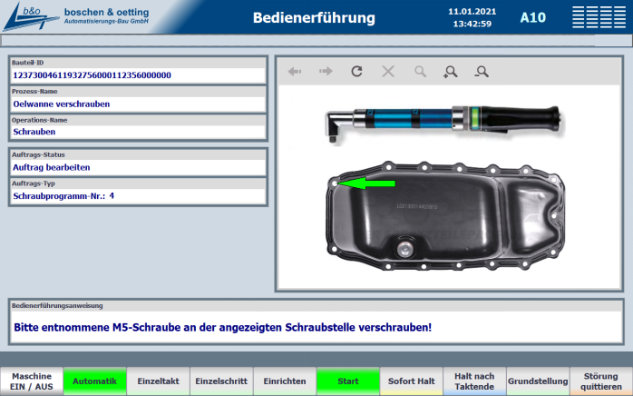
Abbildung 4: Bedienerführung auf einem 12 Zoll Touchpanel
Bedienerführung
Jeder Arbeitsplatz verfügt über ein 12 Zoll Bedienpult . Neben der gängigen Bedienung und Visualisierung beinhaltet das Pult auch eine Bedienerführung.
Die Bedienerführungsanweisungen werden im Konfigurator vorgegeben. Die dazugehörigen Bedienbilder befinden sich auf einer im Bedienpult gesteckten SD-Speicherkarte und können vom Anlagenbetreiber auch flexibel angepasst oder ausgetauscht werden.
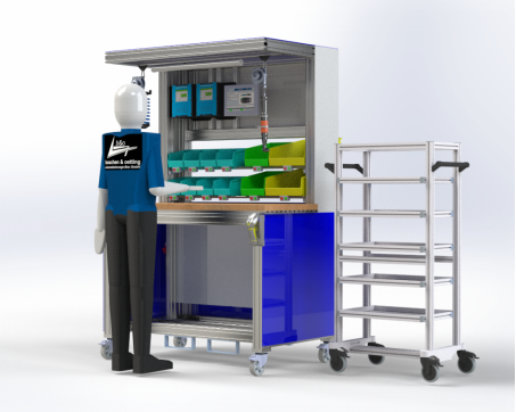
Einsatzbeispiele
Einfach: Schraubstation mit Handscanner
Abbildung 5: Einfach mit Handscanner
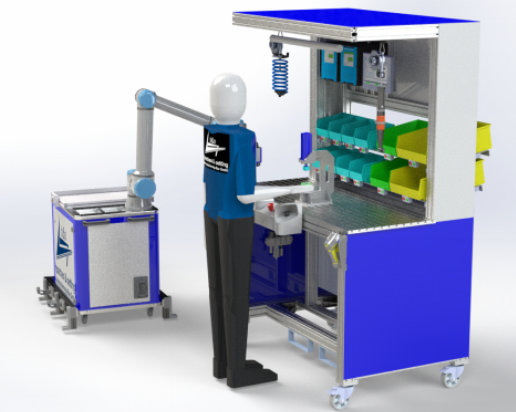
Abbildung 6: Mit MRK Roboter
Mit MRK-Roboter, Fügestation und Schrauber
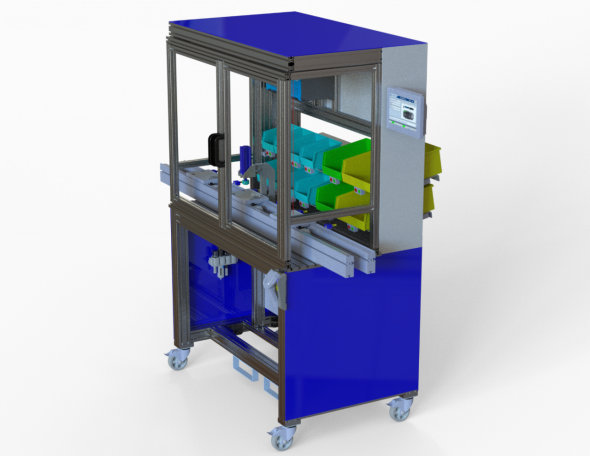